Tecnologia di fusione
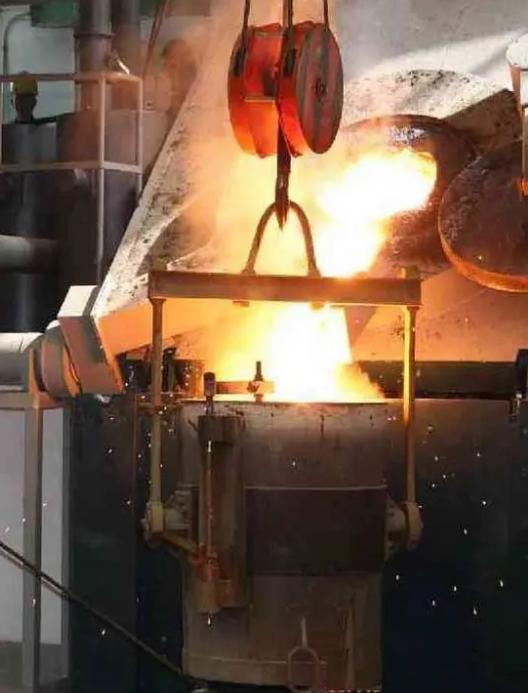
Allo stato attuale, la fusione dei prodotti per la lavorazione del rame adotta generalmente forni fusori a induzione e adotta anche la fusione con forno a riverbero e la fusione con forno a tino.
Il forno di fusione a induzione è adatto a tutti i tipi di rame e leghe di rame e presenta le caratteristiche di una fusione pulita e di garanzia della qualità della fusione.In base alla struttura del forno, i forni a induzione sono suddivisi in forni a induzione a nucleo e forni a induzione a nucleo.Il forno ad induzione con nucleo ha le caratteristiche di elevata efficienza produttiva ed elevata efficienza termica ed è adatto alla fusione continua di un'unica varietà di rame e leghe di rame, come rame rosso e ottone.Il forno a induzione senza crogiolo ha le caratteristiche di un'elevata velocità di riscaldamento e di una facile sostituzione delle varietà di leghe.È adatto alla fusione di rame e leghe di rame ad alto punto di fusione e di varie varietà, come bronzo e cupronichel.
Il forno ad induzione sotto vuoto è un forno ad induzione dotato di un sistema a vuoto, adatto per la fusione di rame e leghe di rame facili da inalare e ossidare, come rame privo di ossigeno, bronzo al berillio, bronzo allo zirconio, bronzo al magnesio, ecc. per vuoto elettrico.
La fusione con forno a riverbero può raffinare e rimuovere le impurità dalla fusione e viene utilizzata principalmente nella fusione di rottami di rame.Il forno a tino è un tipo di forno a fusione rapida e continua, che presenta i vantaggi di un'elevata efficienza termica, un'elevata velocità di fusione e un comodo spegnimento del forno.Può essere controllato;non esiste un processo di raffinazione, quindi la stragrande maggioranza delle materie prime deve essere rame catodico.I forni a tino vengono generalmente utilizzati con macchine di colata continua per la colata continua e possono essere utilizzati anche con forni di attesa per la colata semicontinua.
La tendenza allo sviluppo della tecnologia di produzione della fusione del rame si riflette principalmente nella riduzione della perdita di combustione delle materie prime, nella riduzione dell'ossidazione e dell'inalazione della fusione, nel miglioramento della qualità della fusione e nell'adozione di un'elevata efficienza (la velocità di fusione del forno a induzione è maggiore superiore a 10 t/h), su larga scala (la capacità del forno a induzione può essere superiore a 35 t/set), lunga durata (la durata del rivestimento è da 1 a 2 anni) e risparmio energetico (il consumo energetico del forno a induzione forno è inferiore a 360 kW h/t), il forno di attesa è dotato di un dispositivo di degasaggio (degasaggio del gas CO) e il forno a induzione. Il sensore adotta una struttura a spruzzo, l'apparecchiatura di controllo elettrico adotta un tiristore bidirezionale più un alimentatore a conversione di frequenza, il preriscaldamento del forno, monitoraggio delle condizioni del forno e della temperatura del refrattario e sistema di allarme, il forno di attesa è dotato di un dispositivo di pesatura e il controllo della temperatura è più accurato.
Attrezzature di produzione - Linea di taglio
La produzione della linea di taglio di nastri di rame è una linea di produzione continua di taglio e taglio che allarga l'ampia bobina attraverso lo svolgitore, taglia la bobina nella larghezza richiesta attraverso la macchina da taglio e la riavvolge in più bobine attraverso l'avvolgitore. (Rack di stoccaggio) Utilizzare una gru per riporre i rotoli sullo scaffale di stoccaggio
↓
(Carrello di carico) Utilizzare il carrello di alimentazione per posizionare manualmente il rotolo di materiale sul tamburo svolgitore e serrarlo
↓
(Svolgitore e rullo pressore antiallentamento) Svolgere la bobina con l'aiuto della guida di apertura e del rullo pressore
↓
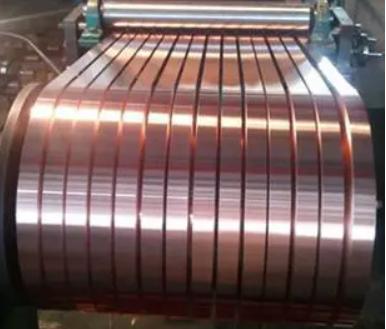
(NO·1 looper e ponte girevole) memorizzazione e buffer
↓
(Dispositivo guida bordo e rullo pressore) I rulli verticali guidano il foglio nei rulli pressori per evitare deviazioni, la larghezza e il posizionamento del rullo guida verticale sono regolabili
↓
(Macchina da taglio) entra nella macchina da taglio per il posizionamento e il taglio
↓
(Sede rotante a cambio rapido) Scambio gruppo utensili
↓
(Dispositivo avvolgitore di rottami) Tagliare il rottame
↓(Tavola guida dell'estremità di uscita e fermo della coda della bobina) Introdurre il crochet N.2
↓
(ponte girevole e crochet N.2) stoccaggio del materiale ed eliminazione della differenza di spessore
↓
(Dispositivo di separazione della tensione della piastra di pressione e dell'albero di espansione dell'aria) fornisce forza di tensione, separazione della piastra e della cinghia
↓
(Csoia da taglio, dispositivo di misurazione della lunghezza dello sterzo e tavola di guida) misurazione della lunghezza, segmentazione della bobina a lunghezza fissa, guida per l'infilatura del nastro
↓
(avvolgitore, dispositivo di separazione, dispositivo a piastra di spinta) nastro separatore, avvolgimento
↓
(scarico camion, imballaggio) scarico e imballaggio con nastro di rame
Tecnologia di laminazione a caldo
La laminazione a caldo viene utilizzata principalmente per la laminazione di billette di lingotti per la produzione di lamiere, nastri e fogli.
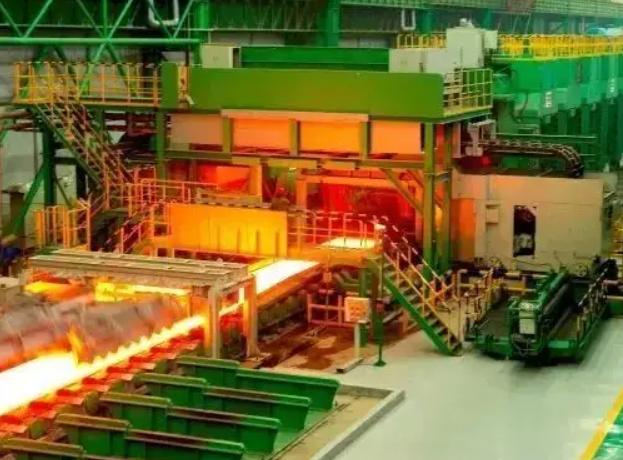
Le specifiche dei lingotti per la laminazione delle billette dovrebbero considerare fattori quali la varietà del prodotto, la scala di produzione, il metodo di fusione, ecc. e sono correlate alle condizioni dell'attrezzatura di laminazione (come apertura del rullo, diametro del rullo, pressione di laminazione consentita, potenza del motore e lunghezza della rulliera) , eccetera. .Generalmente, il rapporto tra lo spessore del lingotto e il diametro del rullo è 1: (3,5~7): la larghezza è solitamente uguale o più volte la larghezza del prodotto finito e la larghezza e la quantità di rifilatura devono essere adeguate considerato.In generale, la larghezza della soletta dovrebbe essere pari all'80% della lunghezza del corpo del rotolo.La lunghezza del lingotto dovrebbe essere ragionevolmente considerata in base alle condizioni di produzione.In generale, presupponendo che la temperatura finale della laminazione a caldo possa essere controllata, quanto più lungo è il lingotto, tanto maggiori saranno l'efficienza e la resa produttiva.
Le specifiche dei lingotti degli impianti di lavorazione del rame di piccole e medie dimensioni sono generalmente (60 ~ 150) mm × (220 ~ 450) mm × (2000 ~ 3200) mm e il peso del lingotto è 1,5 ~ 3 t;le specifiche del lingotto dei grandi impianti di lavorazione del rame Generalmente, è (150~250)mm×(630~1250)mm×(2400~8000)mm, e il peso del lingotto è 4,5~20 t.
Durante la laminazione a caldo, la temperatura della superficie del rullo aumenta notevolmente nel momento in cui il rullo entra in contatto con il pezzo di laminazione ad alta temperatura.L'espansione termica ripetuta e la contrazione a freddo causano crepe e crepe sulla superficie del rotolo.Pertanto, il raffreddamento e la lubrificazione devono essere eseguiti durante la laminazione a caldo.Di solito, come mezzo di raffreddamento e lubrificazione viene utilizzata acqua o un'emulsione a concentrazione inferiore.La velocità di lavorazione totale della laminazione a caldo è generalmente compresa tra il 90% e il 95%.Lo spessore del nastro laminato a caldo è generalmente compreso tra 9 e 16 mm.La fresatura superficiale del nastro dopo la laminazione a caldo può rimuovere strati superficiali di ossido, intrusioni di scaglie e altri difetti superficiali prodotti durante la fusione, il riscaldamento e la laminazione a caldo.A seconda della gravità dei difetti superficiali del nastro laminato a caldo e delle esigenze del processo, la quantità di fresatura su ciascun lato varia da 0,25 a 0,5 mm.
I laminatoi a caldo sono generalmente laminatoi a inversione a due o quattro unità.Con l'allargamento del lingotto e il continuo allungamento della lunghezza del nastro, il livello di controllo e la funzione del laminatoio a caldo hanno una tendenza al continuo miglioramento e miglioramento, come l'uso del controllo automatico dello spessore, rulli piegatori idraulici, anteriori e posteriori rulli verticali, solo rulli di raffreddamento senza raffreddamento Dispositivo di rotolamento, controllo della corona del rullo TP (Taper Piston Roll), tempra in linea (tempra) dopo la laminazione, avvolgimento in linea e altre tecnologie per migliorare l'uniformità della struttura e delle proprietà del nastro e ottenere una migliore piatto.
Tecnologia di fusione
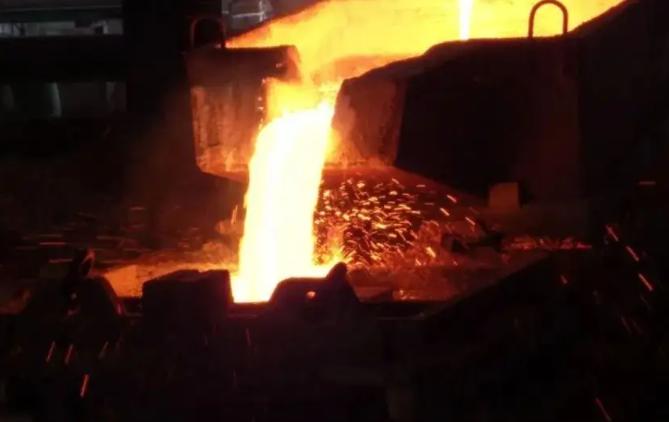
La colata del rame e delle leghe di rame viene generalmente suddivisa in: colata semicontinua verticale, colata continua piena verticale, colata continua orizzontale, colata continua verso l'alto e altre tecnologie di colata.
A. Colata semicontinua verticale
La colata semicontinua verticale ha le caratteristiche di un'attrezzatura semplice e di una produzione flessibile ed è adatta per la colata di vari lingotti rotondi e piatti di rame e leghe di rame.La modalità di trasmissione della macchina di colata semicontinua verticale è suddivisa in idraulica, vite e fune metallica.Poiché la trasmissione idraulica è relativamente stabile, è stata maggiormente utilizzata.Il cristallizzatore può essere vibrato con ampiezze e frequenze diverse a seconda delle esigenze.Attualmente, il metodo di colata semicontinua è ampiamente utilizzato nella produzione di lingotti di rame e leghe di rame.
B. Colata continua completa verticale
La colata continua verticale completa ha le caratteristiche di grande produttività e resa elevata (circa il 98%), adatta per la produzione continua e su larga scala di lingotti con un'unica varietà e specifica, e sta diventando uno dei principali metodi di selezione per la fusione e la colata processo su moderne linee di produzione di nastri di rame su larga scala.Lo stampo per colata continua verticale completa adotta il controllo automatico del livello del liquido laser senza contatto.La macchina di colata adotta generalmente il bloccaggio idraulico, la trasmissione meccanica, il taglio a secco di trucioli a secco raffreddato ad olio in linea e la raccolta dei trucioli, la marcatura automatica e l'inclinazione del lingotto.La struttura è complessa e il grado di automazione è elevato.
C. Colata continua orizzontale
La colata continua orizzontale può produrre billette e billette di filo.
La colata continua orizzontale di nastri può produrre nastri di rame e leghe di rame con uno spessore di 14-20 mm.I nastri in questo intervallo di spessore possono essere laminati direttamente a freddo senza laminazione a caldo, quindi vengono spesso utilizzati per produrre leghe difficili da laminare a caldo (come stagno, bronzo fosforoso, ottone al piombo, ecc.), possono anche produrre ottone, nastro di cupronichel e lega di rame a bassa lega.A seconda della larghezza della striscia di colata, la colata continua orizzontale può colare da 1 a 4 strisce contemporaneamente.Le macchine di colata continua orizzontali comunemente utilizzate possono colare due nastri contemporaneamente, ciascuno con una larghezza inferiore a 450 mm, oppure colare un nastro con una larghezza di 650-900 mm.La striscia di colata continua orizzontale adotta generalmente il processo di colata di pull-stop-reverse push e sulla superficie sono presenti linee periodiche di cristallizzazione, che generalmente dovrebbero essere eliminate mediante fresatura.Esistono esempi domestici di nastri di rame ad alta superficie che possono essere prodotti mediante trafilatura e fusione di billette di nastro senza fresatura.
La colata continua orizzontale di billette di tubi, barre e fili può fondere da 1 a 20 lingotti contemporaneamente in base a diverse leghe e specifiche.Generalmente, il diametro della barra o del filo grezzo è compreso tra 6 e 400 mm e il diametro esterno del tubo grezzo è compreso tra 25 e 300 mm.Lo spessore della parete è di 5-50 mm e la lunghezza del lato del lingotto è di 20-300 mm.I vantaggi del metodo di colata continua orizzontale sono che il processo è breve, i costi di produzione sono bassi e l’efficienza produttiva è elevata.Allo stesso tempo, è anche un metodo di produzione necessario per alcuni materiali in lega con scarsa lavorabilità a caldo.Recentemente, è il metodo principale per realizzare billette di prodotti in rame di uso comune come nastri di bronzo allo stagno-fosforo, nastri di lega di zinco-nichel e tubi di condizionamento d'aria in rame disossidato al fosforo.metodi di produzione.
Gli svantaggi del metodo di produzione della colata continua orizzontale sono: le varietà di leghe adatte sono relativamente semplici, il consumo di materiale di grafite nel manicotto interno dello stampo è relativamente elevato e l'uniformità della struttura cristallina della sezione trasversale del lingotto non lo è facile da controllare.La parte inferiore del lingotto viene continuamente raffreddata per effetto della gravità, che è vicina alla parete interna dello stampo, ed i grani risultano più fini;la parte superiore è dovuta alla formazione di traferri e all'elevata temperatura di fusione, che provoca un ritardo nella solidificazione del lingotto, che rallenta la velocità di raffreddamento e rende l'isteresi di solidificazione del lingotto.La struttura cristallina è relativamente grossolana, cosa particolarmente evidente per i lingotti di grandi dimensioni.Tenuto conto di tali inconvenienti, è attualmente in fase di sviluppo il metodo di fusione a flessione verticale con billetta.Un'azienda tedesca ha utilizzato una colata continua a piegatura verticale per testare la colata di nastri di bronzo allo stagno (16-18) mm × 680 mm come DHP e CuSn6 a una velocità di 600 mm/min.
D. Colata continua verso l'alto
La colata continua verso l'alto è una tecnologia di colata che si è sviluppata rapidamente negli ultimi 20-30 anni ed è ampiamente utilizzata nella produzione di billette per vergelle di rame lucido.Utilizza il principio della fusione con aspirazione sottovuoto e adotta la tecnologia stop-pull per realizzare la fusione continua multitesta.Ha le caratteristiche di un'attrezzatura semplice, un piccolo investimento, una minore perdita di metallo e procedure a basso inquinamento ambientale.La colata continua verso l'alto è generalmente adatta per la produzione di billette di rame rosso e filo di rame privo di ossigeno.Il nuovo risultato sviluppato negli ultimi anni è la sua divulgazione e applicazione in tubi grezzi di grande diametro, ottone e cupronichel.Attualmente è stata sviluppata un'unità di colata continua verso l'alto con una produzione annua di 5.000 t e un diametro superiore a Φ100 mm;Sono state prodotte billette binarie di filo di ottone ordinario e lega ternaria di rame bianco-zinco e la resa delle billette di filo può raggiungere oltre il 90%.
E. Altre tecniche di fusione
La tecnologia della billetta a colata continua è in fase di sviluppo.Supera i difetti come i segni di fiammatura formati sulla superficie esterna della billetta a causa del processo stop-pull della colata continua ascendente e la qualità della superficie è eccellente.E grazie alle sue caratteristiche di solidificazione quasi direzionali, la struttura interna è più uniforme e pura, quindi anche le prestazioni del prodotto sono migliori.La tecnologia di produzione della billetta di filo di rame a colata continua del tipo a nastro è stata ampiamente utilizzata in grandi linee di produzione superiori a 3 tonnellate.La sezione trasversale della bramma è generalmente superiore a 2000 mm2, ed è seguita da un laminatoio continuo ad alta efficienza produttiva.
Nel mio paese è stata sperimentata la fusione elettromagnetica già negli anni '70, ma la produzione industriale non è stata realizzata.Negli ultimi anni, la tecnologia della fusione elettromagnetica ha fatto grandi progressi.Allo stato attuale, sono stati fusi con successo lingotti di rame privi di ossigeno di Φ200 mm con superficie liscia.Allo stesso tempo, l'effetto di agitazione del campo elettromagnetico sulla fusione può favorire la rimozione dei gas di scarico e delle scorie e si può ottenere rame privo di ossigeno con un contenuto di ossigeno inferiore allo 0,001%.
La direzione della nuova tecnologia di fusione della lega di rame è quella di migliorare la struttura dello stampo attraverso la solidificazione direzionale, la solidificazione rapida, la formatura semisolida, l'agitazione elettromagnetica, il trattamento metamorfico, il controllo automatico del livello del liquido e altri mezzi tecnici secondo la teoria della solidificazione., densificazione, purificazione e realizzazione di operazioni continue e formatura quasi finale.
A lungo termine, la fusione di rame e leghe di rame sarà la coesistenza della tecnologia di colata semicontinua e della tecnologia di colata continua completa, e la percentuale di applicazione della tecnologia di colata continua continuerà ad aumentare.
Tecnologia di laminazione a freddo
Secondo le specifiche del nastro laminato e il processo di laminazione, la laminazione a freddo è suddivisa in fioritura, laminazione intermedia e laminazione di finitura.Il processo di laminazione a freddo del nastro fuso con uno spessore da 14 a 16 mm e della billetta laminata a caldo con uno spessore da circa 5 a 16 mm a 2 a 6 mm è chiamato blumitura e il processo di continua riduzione dello spessore del il pezzo laminato è chiamato laminazione intermedia., la laminazione finale a freddo per soddisfare i requisiti del prodotto finito è chiamata laminazione di finitura.
Il processo di laminazione a freddo deve controllare il sistema di riduzione (velocità di lavorazione totale, velocità di lavorazione del passaggio e velocità di lavorazione del prodotto finito) in base alle diverse leghe, specifiche di laminazione e requisiti prestazionali del prodotto finito, selezionare e regolare ragionevolmente la forma del rullo e selezionare ragionevolmente la lubrificazione metodo e lubrificante.Misurazione e regolazione della tensione.
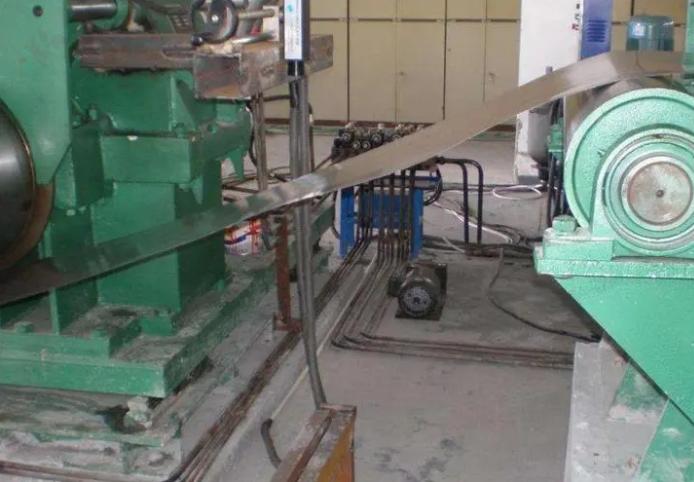
I laminatoi a freddo utilizzano generalmente laminatoi a inversione a quattro o più alti.I moderni laminatoi a freddo utilizzano generalmente una serie di tecnologie come la piegatura idraulica positiva e negativa dei rulli, il controllo automatico dello spessore, della pressione e della tensione, il movimento assiale dei rulli, il raffreddamento segmentale dei rulli, il controllo automatico della forma delle piastre e l'allineamento automatico dei pezzi laminati. , in modo che la precisione della striscia possa essere migliorata.Fino a 0,25±0,005 mm ed entro 5I dalla forma della piastra.
La tendenza allo sviluppo della tecnologia di laminazione a freddo si riflette nello sviluppo e nell'applicazione di laminatoi multi-laminatoio ad alta precisione, velocità di laminazione più elevate, controllo più accurato dello spessore e della forma del nastro e tecnologie ausiliarie come raffreddamento, lubrificazione, avvolgimento, centratura e laminazione rapida. modifica.raffinamento, ecc.
Attrezzature di produzione: forno a campana
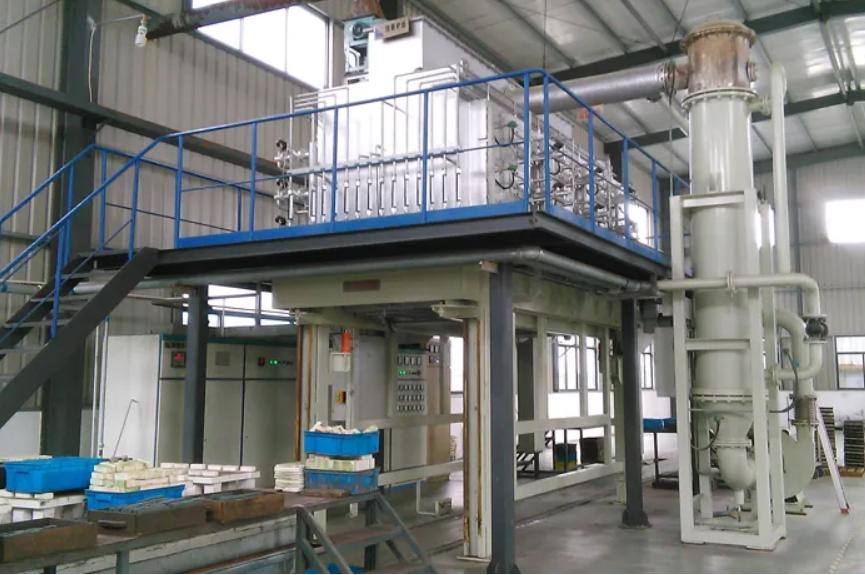
I forni a campana e i forni a sollevamento vengono generalmente utilizzati nella produzione industriale e nelle prove pilota.In generale, la potenza è elevata e il consumo energetico è elevato.Per le imprese industriali, il materiale del forno di sollevamento Luoyang Sigma è la fibra ceramica, che ha un buon effetto di risparmio energetico, un basso consumo energetico e un basso consumo energetico.Risparmia elettricità e tempo, il che è vantaggioso per aumentare la produzione.
Venticinque anni fa, la tedesca BRANDS e Philips, un'azienda leader nel settore della produzione della ferrite, hanno sviluppato congiuntamente una nuova macchina per la sinterizzazione.Lo sviluppo di questa apparecchiatura soddisfa le esigenze speciali dell'industria della ferrite.Durante questo processo, BRANDS Bell Furnace viene continuamente aggiornato.
Presta attenzione alle esigenze di aziende di fama mondiale come Philips, Siemens, TDK, FDK, ecc., che traggono grandi vantaggi anche dalle apparecchiature di alta qualità di BRANDS.
Grazie all'elevata stabilità dei prodotti realizzati dai forni a campana, i forni a campana sono diventati le migliori aziende nel settore della produzione professionale di ferrite.Venticinque anni fa, il primo forno realizzato da BRANDS produce ancora prodotti di alta qualità per Philips.
La caratteristica principale del forno di sinterizzazione offerto dal forno a campana è la sua elevata efficienza.Il suo sistema di controllo intelligente e le altre apparecchiature formano un'unità funzionale completa, in grado di soddisfare pienamente i requisiti quasi all'avanguardia dell'industria della ferrite.
I clienti dei forni a campana possono programmare e memorizzare qualsiasi profilo di temperatura/atmosfera richiesto per produrre prodotti di alta qualità.Inoltre, i clienti possono anche produrre qualsiasi altro prodotto in tempo in base alle esigenze effettive, abbreviando così i tempi di consegna e riducendo i costi.L'attrezzatura di sinterizzazione deve avere una buona adattabilità per produrre una varietà di prodotti diversi per adattarsi continuamente alle esigenze del mercato.Ciò significa che i prodotti corrispondenti devono essere realizzati in base alle esigenze del singolo cliente.
Un buon produttore di ferrite può produrre più di 1000 magneti diversi per soddisfare le esigenze speciali dei clienti.Questi richiedono la capacità di ripetere il processo di sinterizzazione con elevata precisione.I sistemi di forni a campana sono diventati forni standard per tutti i produttori di ferrite.
Nell'industria della ferrite, questi forni vengono utilizzati principalmente per ferrite a basso consumo energetico e ad alto valore μ, soprattutto nel settore delle comunicazioni.È impossibile produrre nuclei di alta qualità senza un forno a campana.
Il forno a campana richiede solo pochi operatori durante la sinterizzazione, il carico e lo scarico possono essere completati durante il giorno e la sinterizzazione può essere completata di notte, consentendo un picco di risparmio energetico, il che è molto pratico nell'attuale situazione di carenza di energia.I forni a campana producono prodotti di alta qualità e tutti gli investimenti aggiuntivi vengono rapidamente recuperati grazie a prodotti di alta qualità.Il controllo della temperatura e dell'atmosfera, la progettazione del forno e il controllo del flusso d'aria all'interno del forno sono tutti perfettamente integrati per garantire un riscaldamento e un raffreddamento uniformi del prodotto.Il controllo dell'atmosfera del forno durante il raffreddamento è direttamente correlato alla temperatura del forno e può garantire un contenuto di ossigeno pari allo 0,005% o anche inferiore.E queste sono cose che i nostri concorrenti non possono fare.
Grazie al completo sistema di input di programmazione alfanumerica, è possibile replicare facilmente lunghi processi di sinterizzazione, garantendo così la qualità del prodotto.Quando si vende un prodotto, si riflette anche la qualità del prodotto.
Tecnologia del trattamento termico
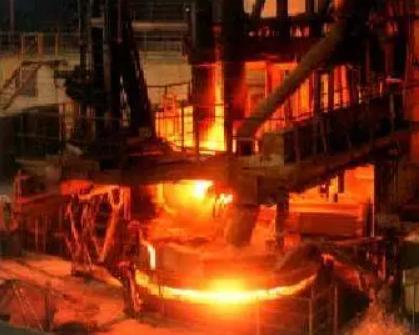
Alcuni lingotti (strisce) di lega con grave segregazione dei dendriti o stress di fusione, come il bronzo allo stagno-fosforo, devono essere sottoposti a una speciale ricottura di omogeneizzazione, che viene generalmente eseguita in un forno a campana.La temperatura di ricottura di omogeneizzazione è generalmente compresa tra 600 e 750°C.
Allo stato attuale, la maggior parte della ricottura intermedia (ricottura di ricristallizzazione) e della ricottura finita (ricottura per controllare lo stato e le prestazioni del prodotto) dei nastri in lega di rame sono ricotti in bianco mediante protezione dai gas.I tipi di forni includono forni a campana, forni a cuscino d'aria, forni a trazione verticale, ecc. La ricottura ossidativa è in fase di eliminazione.
La tendenza allo sviluppo della tecnologia del trattamento termico si riflette nel trattamento in linea di laminazione a caldo di materiali in lega rinforzati per precipitazione e nella successiva tecnologia di trattamento termico per deformazione, ricottura in bianco continua e ricottura in tensione in atmosfera protettiva.
Tempra: il trattamento termico di invecchiamento viene utilizzato principalmente per il rafforzamento trattabile termicamente delle leghe di rame.Attraverso il trattamento termico, il prodotto cambia la sua microstruttura e ottiene le proprietà speciali richieste.Con lo sviluppo di leghe ad alta resistenza e alta conduttività, il processo di trattamento termico di tempra e invecchiamento verrà maggiormente applicato.L'attrezzatura per il trattamento dell'invecchiamento è più o meno la stessa dell'attrezzatura per la ricottura.
Tecnologia di estrusione
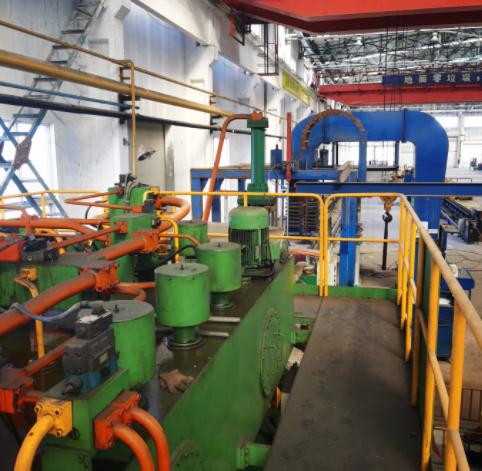
L'estrusione è un metodo maturo e avanzato per la produzione di tubi, barre, profili e fornitura di billette in rame e leghe di rame.Cambiando la matrice o utilizzando il metodo dell'estrusione a perforazione, è possibile estrudere direttamente varie varietà di leghe e diverse forme di sezione trasversale.Attraverso l'estrusione, la struttura fusa del lingotto viene trasformata in una struttura lavorata e la billetta del tubo estruso e la billetta della barra hanno un'elevata precisione dimensionale e la struttura è fine e uniforme.Il metodo di estrusione è un metodo di produzione comunemente utilizzato dai produttori nazionali ed esteri di tubi e barre di rame.
La forgiatura delle leghe di rame viene eseguita principalmente dai produttori di macchinari nel mio paese, tra cui principalmente la forgiatura libera e la forgiatura a stampo, come ingranaggi di grandi dimensioni, ingranaggi a vite senza fine, viti senza fine, anelli di ingranaggi sincronizzatori di automobili, ecc.
Il metodo di estrusione può essere suddiviso in tre tipologie: estrusione diretta, estrusione inversa ed estrusione speciale.Tra questi, ci sono molte applicazioni di estrusione diretta, l'estrusione inversa viene utilizzata nella produzione di barre e fili di piccole e medie dimensioni e l'estrusione speciale viene utilizzata nella produzione speciale.
Durante l'estrusione, in base alle proprietà della lega, ai requisiti tecnici dei prodotti estrusi, alla capacità e alla struttura dell'estrusore, il tipo, le dimensioni e il coefficiente di estrusione del lingotto dovrebbero essere ragionevolmente selezionati, in modo che il grado di deformazione sia non meno dell'85%.La temperatura di estrusione e la velocità di estrusione sono i parametri di base del processo di estrusione e l'intervallo ragionevole di temperatura di estrusione deve essere determinato in base al diagramma di plasticità e al diagramma di fase del metallo.Per il rame e le leghe di rame, la temperatura di estrusione è generalmente compresa tra 570 e 950 °C, e la temperatura di estrusione dal rame arriva addirittura tra 1000 e 1050 °C.Rispetto alla temperatura di riscaldamento del cilindro di estrusione compresa tra 400 e 450 °C, la differenza di temperatura tra i due è relativamente elevata.Se la velocità di estrusione è troppo lenta, la temperatura della superficie del lingotto scenderà troppo velocemente, con conseguente aumento delle irregolarità del flusso del metallo, che porterà ad un aumento del carico di estrusione e causerà persino un fenomeno di noia. .Pertanto, il rame e le leghe di rame utilizzano generalmente un'estrusione ad alta velocità, la velocità di estrusione può raggiungere più di 50 mm/s.
Quando si estrudono rame e leghe di rame, viene spesso utilizzata l'estrusione di pelatura per rimuovere i difetti superficiali del lingotto e lo spessore di pelatura è di 1-2 m.La sigillatura con acqua viene generalmente utilizzata all'uscita della billetta di estrusione, in modo che il prodotto possa essere raffreddato nel serbatoio dell'acqua dopo l'estrusione e la superficie del prodotto non venga ossidata e la successiva lavorazione a freddo possa essere eseguita senza decapaggio.Si tende a utilizzare un estrusore di grande tonnellaggio con un dispositivo di avvolgimento sincrono per estrudere bobine di tubi o fili con un peso singolo superiore a 500 kg, in modo da migliorare efficacemente l'efficienza produttiva e la resa complessiva della sequenza successiva.Attualmente, la produzione di tubi in rame e leghe di rame adotta principalmente estrusori idraulici orizzontali con sistema di perforazione indipendente (a doppia azione) e trasmissione diretta della pompa dell'olio, mentre la produzione di barre adotta principalmente sistemi di perforazione non indipendenti (a singola azione) e trasmissione diretta della pompa dell'olio.Estrusore idraulico orizzontale avanti o indietro.Le specifiche degli estrusori comunemente utilizzati sono 8-50 MN, e ora tende ad essere prodotto da estrusori di grande tonnellaggio superiori a 40 MN per aumentare il peso singolo del lingotto, migliorando così l'efficienza e la resa della produzione.
I moderni estrusori idraulici orizzontali sono strutturalmente dotati di telaio integrale precompresso, guida e supporto a "X" del cilindro di estrusione, sistema di perforazione integrato, raffreddamento interno dell'ago di perforazione, set di matrici scorrevoli o rotanti e dispositivo di cambio rapido delle matrici, pompa dell'olio variabile ad alta potenza diretta azionamento, valvola logica integrata, controllo PLC e altre tecnologie avanzate, l'apparecchiatura ha alta precisione, struttura compatta, funzionamento stabile, interblocco sicuro e controllo del programma facile da realizzare.La tecnologia dell'estrusione continua (Conform) ha fatto alcuni progressi negli ultimi dieci anni, soprattutto per la produzione di barre di forma speciale come i cavi delle locomotive elettriche, il che è molto promettente.Negli ultimi decenni, la nuova tecnologia di estrusione si è sviluppata rapidamente e la tendenza di sviluppo della tecnologia di estrusione è incarnata come segue: (1) Attrezzature per estrusione.La forza di estrusione della pressa per estrusione si svilupperà in una direzione maggiore e la pressa per estrusione da oltre 30 MN diventerà il corpo principale e l'automazione della linea di produzione della pressa per estrusione continuerà a migliorare.Le moderne macchine di estrusione hanno adottato completamente il controllo del programma computerizzato e il controllo logico programmabile, in modo che l'efficienza produttiva sia notevolmente migliorata, gli operatori siano significativamente ridotti ed è persino possibile realizzare il funzionamento automatico senza operatore delle linee di produzione di estrusione.
Anche la struttura del corpo dell'estrusore è stata continuamente migliorata e perfezionata.Negli ultimi anni alcuni estrusori orizzontali hanno adottato un telaio precompresso per garantire la stabilità della struttura complessiva.Il moderno estrusore realizza i metodi di estrusione diretta e inversa.L'estrusore è dotato di due alberi di estrusione (albero di estrusione principale e albero della filiera).Durante l'estrusione, il cilindro di estrusione si muove insieme all'albero principale.In questo momento, il prodotto è La direzione di deflusso è coerente con la direzione di movimento dell'albero principale e opposta alla direzione di movimento relativa dell'asse dello stampo.Anche la base della matrice dell'estrusore adotta la configurazione di stazioni multiple, che non solo facilita il cambio della matrice, ma migliora anche l'efficienza produttiva.Gli estrusori moderni utilizzano un dispositivo di controllo della regolazione della deviazione laser, che fornisce dati efficaci sullo stato della linea centrale di estrusione, utile per una regolazione rapida e tempestiva.La pressa idraulica ad azionamento diretto con pompa ad alta pressione che utilizza l'olio come mezzo di lavoro ha completamente sostituito la pressa idraulica.Anche gli strumenti di estrusione vengono costantemente aggiornati con lo sviluppo della tecnologia di estrusione.L'ago penetrante per il raffreddamento ad acqua interno è stato ampiamente promosso e il perforatore e l'ago rotante a sezione trasversale variabile migliorano notevolmente l'effetto di lubrificazione.Gli stampi in ceramica e gli stampi in acciaio legato con una maggiore durata e una migliore qualità della superficie sono più ampiamente utilizzati.
Anche gli strumenti di estrusione vengono costantemente aggiornati con lo sviluppo della tecnologia di estrusione.L'ago penetrante per il raffreddamento ad acqua interno è stato ampiamente promosso e il perforatore e l'ago rotante a sezione trasversale variabile migliorano notevolmente l'effetto di lubrificazione.L'applicazione di stampi in ceramica e stampi in acciaio legato con una maggiore durata e una maggiore qualità della superficie è più popolare.(2) Processo di produzione dell'estrusione.Le varietà e le specifiche dei prodotti estrusi sono in continua espansione.L'estrusione di tubi, barre, profili e profili super-grandi di piccola sezione e ad altissima precisione garantisce la qualità estetica dei prodotti, riduce i difetti interni dei prodotti, riduce la perdita geometrica e promuove ulteriormente metodi di estrusione come prestazioni uniformi degli estrusi prodotti.Anche la moderna tecnologia di estrusione inversa è ampiamente utilizzata.Per i metalli facilmente ossidabili, viene adottata l'estrusione con tenuta ad acqua, che può ridurre l'inquinamento da decapaggio, ridurre la perdita di metallo e migliorare la qualità della superficie dei prodotti.Per i prodotti estrusi che necessitano di tempra è sufficiente controllare la temperatura adeguata.Il metodo di estrusione della tenuta idraulica può raggiungere lo scopo, abbreviare efficacemente il ciclo di produzione e risparmiare energia.
Con il continuo miglioramento della capacità dell'estrusore e della tecnologia di estrusione, è stata gradualmente applicata la moderna tecnologia di estrusione, come l'estrusione isotermica, l'estrusione con matrice di raffreddamento, l'estrusione ad alta velocità e altre tecnologie di estrusione diretta, l'estrusione inversa, l'estrusione idrostatica. L'applicazione pratica della tecnologia di estrusione continua di pressatura e Conform, l'applicazione della tecnologia di estrusione di polveri e di estrusione composita stratificata di materiali superconduttori a bassa temperatura, lo sviluppo di nuovi metodi come l'estrusione di metalli semisolidi e l'estrusione multi-blank, lo sviluppo di piccole parti di precisione Tecnologia di formatura per estrusione a freddo, ecc., sono stati rapidamente sviluppati e ampiamente sviluppati e applicati.
Spettrometro
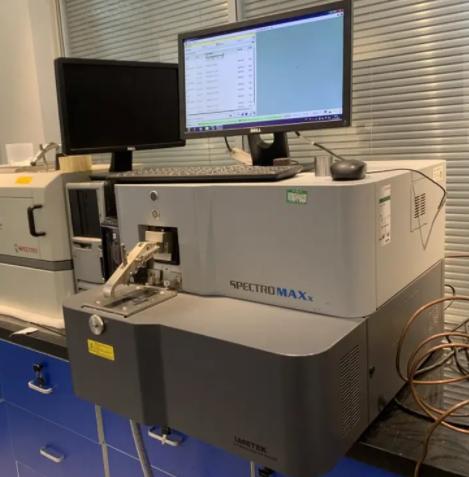
Lo spettroscopio è uno strumento scientifico che decompone la luce con composizione complessa in linee spettrali.La luce a sette colori della luce solare è la parte che l'occhio nudo può distinguere (luce visibile), ma se la luce solare viene scomposta da uno spettrometro e organizzata secondo la lunghezza d'onda, la luce visibile occupa solo una piccola gamma dello spettro e il resto è visibile. spettri non distinguibili ad occhio nudo, come raggi infrarossi, microonde, raggi UV, raggi X, ecc. L'informazione ottica viene catturata dallo spettrometro, sviluppata con una pellicola fotografica, oppure visualizzata ed analizzata da un display automatico computerizzato strumento numerico, in modo da rilevare quali elementi sono contenuti nell'articolo.Questa tecnologia è ampiamente utilizzata nel rilevamento dell'inquinamento atmosferico, dell'acqua, dell'igiene alimentare, dell'industria dei metalli, ecc.
Lo spettrometro, noto anche come spettrometro, è ampiamente noto come spettrometro a lettura diretta.Un dispositivo che misura l'intensità delle linee spettrali a diverse lunghezze d'onda con fotorilevatori come tubi fotomoltiplicatori.È costituito da una fessura di ingresso, un sistema dispersivo, un sistema di imaging e una o più fessure di uscita.La radiazione elettromagnetica della sorgente di radiazione viene separata dall'elemento dispersivo nella lunghezza d'onda richiesta o nella regione di lunghezza d'onda e l'intensità viene misurata alla lunghezza d'onda selezionata (o alla scansione di una determinata banda).Esistono due tipi di monocromatori e policromatori.
Test dello strumento-conduttimetro
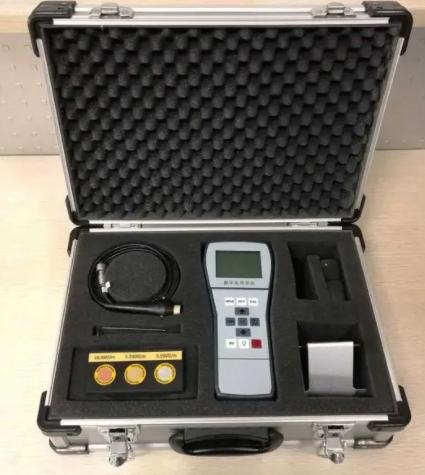
Il misuratore digitale portatile di conducibilità metallica (conduttimetro) FD-101 applica il principio del rilevamento delle correnti parassite ed è appositamente progettato in base ai requisiti di conduttività dell'industria elettrica.Soddisfa gli standard di prova dell'industria dei metalli in termini di funzionalità e precisione.
1. Il conduttimetro a correnti parassite FD-101 ha tre caratteristiche uniche:
1) L'unico conduttimetro cinese che ha superato la verifica dell'Istituto dei Materiali Aeronautici;
2) L'unico conduttimetro cinese in grado di soddisfare le esigenze delle aziende del settore aeronautico;
3) L'unico conduttimetro cinese esportato in molti paesi.
2. Introduzione alla funzione del prodotto:
1) Ampio intervallo di misurazione: 6,9% IACS-110% IACS (4,0 MS/m-64 MS/m), che soddisfa il test di conducibilità di tutti i metalli non ferrosi.
2) Calibrazione intelligente: veloce e precisa, evitando completamente errori di calibrazione manuale.
3) Lo strumento ha una buona compensazione della temperatura: la lettura viene compensata automaticamente al valore a 20 °C e la correzione non è influenzata da errori umani.
4) Buona stabilità: è la tua guardia personale per il controllo qualità.
5) Software intelligente umanizzato: offre una comoda interfaccia di rilevamento e potenti funzioni di elaborazione e raccolta dati.
6) Comodità d'uso: il sito produttivo e il laboratorio possono essere utilizzati ovunque, conquistando il favore della maggior parte degli utenti.
7) Autosostituzione delle sonde: ogni host può essere dotato di più sonde e gli utenti possono sostituirle in qualsiasi momento.
8) Risoluzione numerica: 0,1% IACS (MS/m)
9) L'interfaccia di misurazione visualizza contemporaneamente i valori di misurazione in due unità di %IACS e MS/m.
10) Ha la funzione di contenere i dati di misurazione.
Tester di durezza
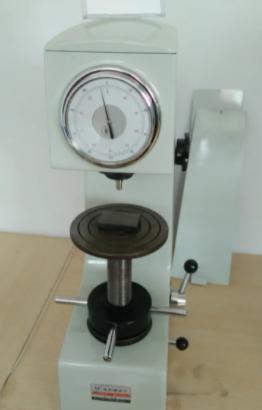
Lo strumento adotta un design unico e preciso nella meccanica, nell'ottica e nella sorgente luminosa, che rende l'immagine dell'indentazione più chiara e la misurazione più accurata.Entrambi gli obiettivi 20x e 40x possono partecipare alla misurazione, ampliando il campo di misurazione e ampliando l'applicazione.Lo strumento è dotato di un microscopio di misurazione digitale, che può visualizzare il metodo di prova, la forza di prova, la lunghezza di rientranza, il valore di durezza, il tempo di mantenimento della forza di prova, i tempi di misurazione, ecc. sullo schermo del liquido e dispone di un'interfaccia filettata che può essere collegata a una fotocamera digitale e una fotocamera CCD.Ha una certa rappresentatività nei prodotti di testa nazionali.
Test del rilevatore di resistività dello strumento
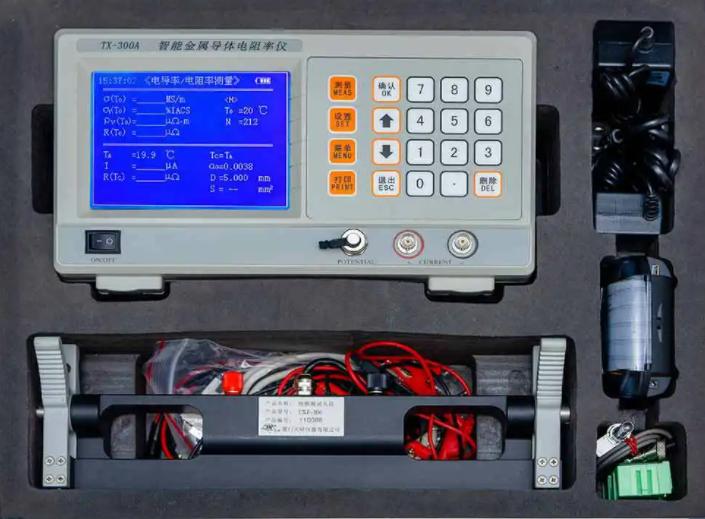
Lo strumento di misura della resistività del filo metallico è uno strumento di prova ad alte prestazioni per parametri quali resistività del filo, della barra e conduttività elettrica.Le sue prestazioni sono pienamente conformi ai requisiti tecnici pertinenti in GB/T3048.2 e GB/T3048.4.Ampiamente usato in metallurgia, energia elettrica, fili e cavi, elettrodomestici, college e università, unità di ricerca scientifica e altre industrie.
Principali caratteristiche dello strumento:
(1) Integra tecnologia elettronica avanzata, tecnologia a chip singolo e tecnologia di rilevamento automatico, con una forte funzione di automazione e un funzionamento semplice;
(2) Basta premere il tasto una volta, tutti i valori misurati possono essere ottenuti senza alcun calcolo, adatti per un rilevamento continuo, veloce e accurato;
(3) Design alimentato a batteria, dimensioni ridotte, facile da trasportare, adatto per l'uso sul campo e sul campo;
(4) Schermo grande, carattere grande, può visualizzare contemporaneamente resistività, conduttività, resistenza e altri valori misurati e temperatura, corrente di prova, coefficiente di compensazione della temperatura e altri parametri ausiliari, molto intuitivi;
(5) Una macchina è multiuso, con 3 interfacce di misurazione, ovvero interfaccia di misurazione della resistività del conduttore e della conducibilità, interfaccia di misurazione completa dei parametri del cavo e interfaccia di misurazione della resistenza CC del cavo (tipo TX-300B);
(6) Ciascuna misurazione ha le funzioni di selezione automatica della corrente costante, commutazione automatica della corrente, correzione automatica del punto zero e correzione automatica della compensazione della temperatura per garantire l'accuratezza di ciascun valore di misurazione;
(7) L'esclusivo dispositivo di prova portatile a quattro terminali è adatto per la misurazione rapida di diversi materiali e diverse specifiche di fili o barre;
(8) Memoria dati incorporata, che può registrare e salvare 1000 set di dati di misurazione e parametri di misurazione e collegarsi al computer superiore per generare un rapporto completo.